Combine Harvester Types - Hybrid CLAAS
- By: "Farm Tender" News
- Machinery & Equipment News
- Sep 20, 2024
- 608 views
- Share
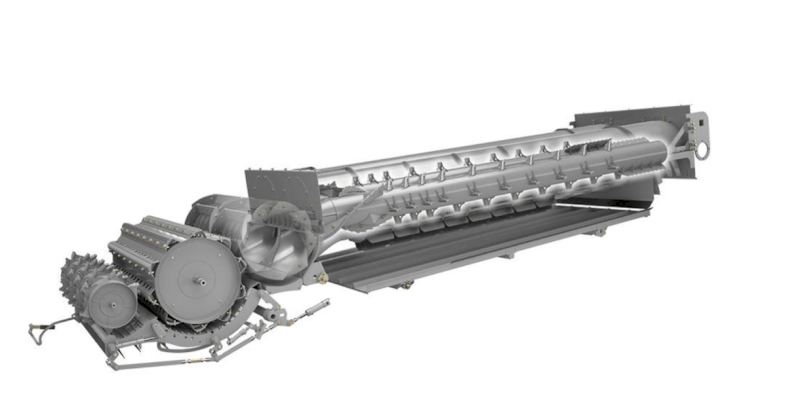
By Phil Rowntree - 0428 659 056 - philr@farmtender.com.au
All modern combines have the same task to achieve, and it is one of the most labour-saving inventions of its time: They are designed to:
- Cut the crop
- Thresh the crop
- Separate the grain from the heads
- Clean the straw and chaff from the grain
Hybrid CLAAS:
Please Note: New Holland offers a hybrid combine being a CH7.70 and although the CH7.70 varies technically in some areas it is still a hybrid machine due to having a threshing cylinder and rotors.
CLAAS launched the first hybrid combine harvester in 1995. Taking the threshing cylinder of a conventional machine with the addition of twin rotors. Known as accelerated pre-separation threshing (branded as APS), and twin rotor separation system.
Approximately 70 per cent of grain separation occurs before the crop reaches the rotors. This allows a hybrid machine to operate more efficiently and longer in all conditions.
As with all combines the crop flows in via the feeder housing. The crop is firstly met by an east/west pegged drum which starts the threshing process. Next the crop enters the threshing cylinder. The threshing cylinder has adjustable RPM and concave gap to accomodate different conditions. Between the threshing cylinder and twin rotors is a “chevron” feeding drum to assist dividing the crop into the rotors.
The “APS” RPM is set by the operator for the threshing cylinder. The pegged drum RPM is less than the cylinder and the Chevron feeding drum RPM is higher than the cylinder. These different RPM settings are said to accelerate the crop from the feeder housing to the twin rotors in a gentler manner.
Once the crop has entered the rotors, the remaining grain is separated by centrifugal force rather than gravity in the spinning motion. Pegs are used in the rotors, and blanking doors can be closed depending on crop type or harvesting conditions.
As stated previously the twin rotors are smaller in diameter than a single rotor machine. Therefore the rotors separating the grain are operating at a higher RPM. This creates more centrifugal force and promotes a higher throughput of material. As per single rotor combines the rotors RPM can be adjusted to suit conditions. A twin rotor machine generally has a longer rotor length than a single rotor machine.
The remaining straw will exit the combine via the rear of the rotors this may pass through a chopper system or directly to the ground in a windrow. Clean grain and chaff etc will fall on to the sieves. As per the conventional combines the use of fans, gravity and adjustable sieves, the remaining chaff is cleaned from the grain. The clean grain then falls through adjustable sieves to be transferred to the grain tank.
It is interesting to note that a CLAAS hybrid combine keeps chaff separate from the straw, and the combine has two spreaders to accommodate this.
Advantages
- High Capacity with lower losses.
- Ability to handle a wide range of crop types.
- Ability to operate in highly variable weather conditions
- Highly adjustable threshing/separation/cleaning
Disadvantages
- High power requirements.
- More moving parts.
- Hard on straw and can pulverise.
- Difficult to unblock.
Share Ag News Via